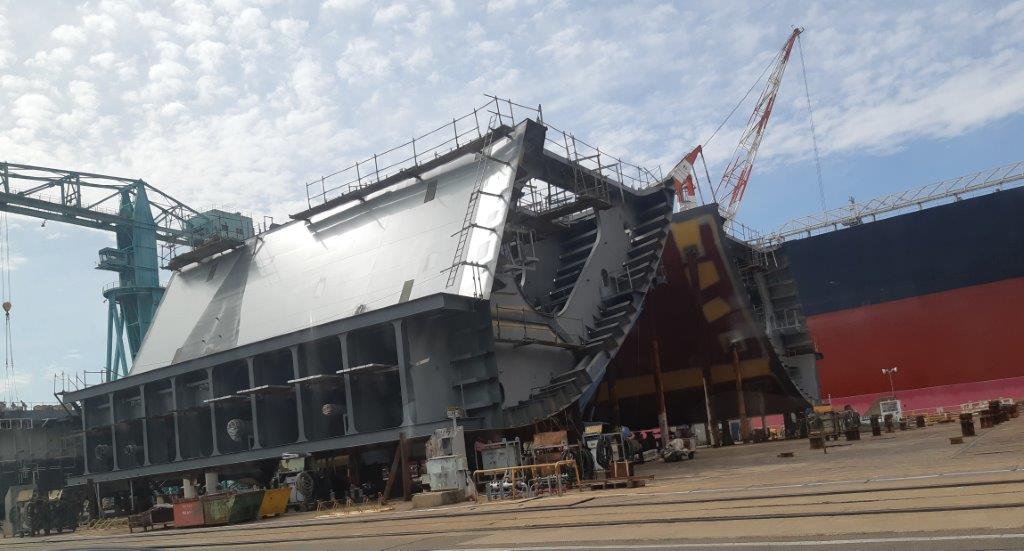
下地加工はOKショットの『岡垣興業株式会社』にお任せください!
下地加工は岡垣興業株式会社にお任せください!
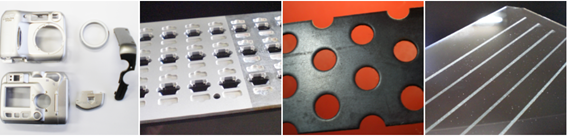
弊社岡垣興業株式会社では、サンドブラスト(略:ブラスト)によるハイクオリティな下地加工を行っております。
製品の塗装や接着をおこなう前の重要な工程が『下地加工』です。これまでの下地処理方法といえば、サンドペーパーやグラインダーによる手作業が基本でした。手作業による下地処理は加工しきれない部分や処理に時間が掛かってしまうこともあります。
コストや時間をかけて下地加工を行なったとしても、処理クオリティが低ければ、次の工程で密着不良や錆の発生などが起こってしまいかねません。製品素材がいかに優れていたとしても、加工処理が正しく行なわれなければ、素材の優位性を活かしきれなくなるのです。
ではどうすればいいのか?それは、処理方法を根本から見なおすことです。つまり、サンドペーパーやグラインダーによる「手作業」での下地処理を『自動化=ブラスト』に変更するのです。
確実に、そして次工程で最大の効果を発揮するためにも重要な『下地加工』。弊社岡垣興業株式会社では、ブラストによるハイクオリティな下地加工を承っております。
下地加工なら岡垣興業株式会社のサンドブラストにおまかせください

製品の下地加工は弊社岡垣興業株式会社のブラストにおまかせください。弊社では製品に合わせてブラスト機器や研磨材を使い分けることで、ハイクオリティな下地加工が可能にしています。
下地加工とは?
下地加工とは製品の塗装前や接着前におこなう加工処理のことです。下地処理が正しく行なわれないと、塗装不良や密着不良が発生したり、錆が浮いてしまったりと散々な状態になってしまいます。
ブラストによる処理効果によって、製品表面を限りなくお客さまの理想に近づけ、製品そのものの寿命も延ばせるのです。定期的なメンテナンスが必要ですが、ブラスト以外の加工方法に比べて長い期間、良い状態を維持できるためコスト削減にもつながるのです。
サンドブラストの下地加工による効果
ブラストによる下地加工は手作業に比べ、作業時間が圧倒的に短縮されます。また処理レベルの精度にばらつきや不安がありません。塗装前や接着前の下地処理では、処理グレードに合わせ処理いたします。下地処理をブラストでおこなうと、製品表面の面積がサンドペーパーやグラインダーなどの下地処理に比べて広くなります。
塗料や接着材がブラスト処理された表面にアンカーパターンが形成され、塗料や接着部分のアンカー効果が密着性をアップするのです。密着性が高いと、処理後の年数経過による塗装剥がれや錆の発生などが抑制されます。
複雑な形状や金属以外の材質でも同じように処理できるのがブラストの強みです。工業製品には細かい箇所や複雑な部分が多くあります。サンドペーパーやグラインダーでは届かない部分の下地処理も、ブラストならば簡単に加工が可能です。
下地加工をサンドブラストでおこなうメリット
ブラストによる下地加工にはメリットが多いです。ここでは主なメリットについて詳しく解説していきます。
• ドライ工法であるため環境に優しい
• 自動化できるため複数製品の下地処理がスピーディにできる
• 複雑な形状・細かい部品の下地処理も可能
• 加工面の粗さ調節ができる
• 加工対象製品の素材に関わらず下地処理ができる
ドライ工法であるため環境に優しい
本来、下地処理には工業用水を使って加工を行なうのが常識です。ブラストは高圧噴射された研磨材が製品表面に加工を施すドライ工法になります。
もともとブラストは、砂嵐で巨大な岩が削れていく様子を参考に生み出された工業技術です。使用済みの研磨材は再利用されるか、使い物にならない場合はそのまま廃棄されます。つまり、下地処理で不純物が混ざった工業用水が垂れ流されることはないのです。
処理方法を誤れば微粒子が大気中にばらまかれてしまい「PM2.5」のような工業公害になってしまいますが、技術大国日本において加工処理で発生したPM2.5を処理するのは難しいことではありません。環境に優しい下地処理こそブラストなのです!
自動化できるため複数製品の下地処理がスピーディにできる
弊社のブラスト機器にはスタッフの手作業以外に、自動による加工も可能です。そのため、ご依頼された製品が複数個であったとしても、スピーディに納品ができます。
下地加工は塗装や接着といった加工の「工程」作業にあたります。下地処理に時間がかかってしまうと、次工程の加工が遅くなってしまい、加工の全工程が遅くなってしまうのです。自動化できる下地処理こそ、ブラストがもっとも得意とする分野なのです!
複雑な形状・細かい部品の下地処理も可能
下地処理が必要な製品の中には、複雑な形状や細かい部品で構成されているものも少なくありません。ペーパーやグラインダーでもこうした製品の下地処理は可能ですが、一度分解した上で処理を行なうことが多いため、時間や人件費といったコストがかかってしまいます。
ブラストで処理を行なえば、分解も最小限で済みますし、なにより自動化できるため、下地処理のコストも削減できます。研磨材は製品によって素材や形状を使い分けなくてはいけません。同じ素材でも粒の大きさを代えることで、複雑な形状や細かい部品の処理をしやすくできるのです。
加工面の粗さ調節ができる
塗装や接着といった、製品表面にプラスアルファを加える加工では、加工面に状態が重要になります。液体塗料であっても、細かい溝が無ければ剥がれやすくなってしまいます。接着の場合も、ある程度の溝が無ければ接着対象と結合するための接着剤が付着しません。
次工程のクオリティを左右するのが下地処理なのです。ブラストでは、研磨材の形状や素材を変更することで『加工面の粗さ調節』が可能です。弊社ではテストブラストの段階で粗さ調節を数段階に分けた試射をおこないます。お客さまの希望とする状態をじかに確認できるのです。
加工対象製品の素材に関わらず下地処理ができる
下地処理が必要なのはなにも金属製の製品とは限りません。プラスチックのようなやわらかいものもあれば、合金のような硬いものもあるでしょう。ブラストは高圧で噴射する研磨材を使います。研磨材の素材や圧力を変えることで、ほとんどの製品は加工可能です。
研磨材の中には最高硬度を誇るダイヤモンドに近い硬度をもつ結晶質ジルコニアなどもあります。製品の素材の硬さや柔らかさでブラストによる下地処理ができるか不安、という場合でも心配無用です。
岡垣興業㈱のサンドブラストはココが違う!
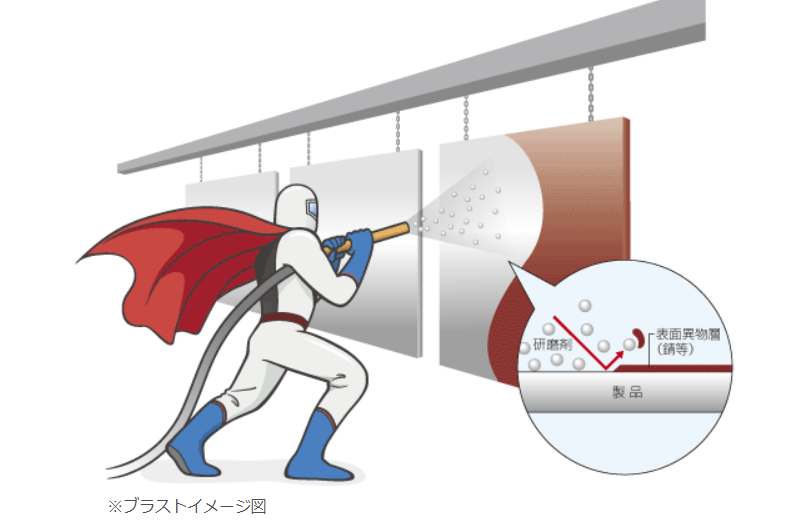
弊社の理念はGrow upです。どんな材質、形状でも挑戦し、お客様の要望に全力で答える。岡垣興業㈱に相談してよかったと言ってもらえるよう日々精進いたします。
使う機器の種類が豊富!

弊社では、大型ブラスト機器はもちろんのこと、細かい部分のブラストも可能な小型機器も各種取り揃えております。弊社のブラスト機器は主に次の8種類です。
• 大型直圧ブラスト
• 特殊タッチパネル式ブラスト
• Labブラスト
• Suction式ブラスト
• 小型自動ブラスト
• パイプ内面ブラスト
• 重力式ブラスト
• バレルブラスト
製品に合わせて各機器を使い分けるため、複雑な箇所や細かい部分の隅々まで下地処理が可能なのです。
研磨材は国際基準に沿って使用!
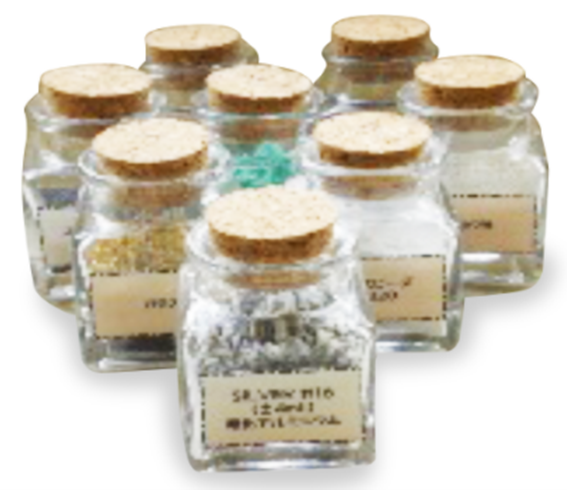
ブラストの命ともいうべき研磨材も、ISO11124-11127標準(国際基準)に沿った製品をご用意しています。下地処理に使われることが多い研磨材は、製品にもよりますがほとんどが高硬度の素材です。
しかし、高硬度の素材ではなくとも、形状を変えることで下地処理を可能にする場合もあります。もともとブラストで使われていた研磨材はケイ素シリカを原料にした珪砂でした。ですが、珪肺と呼ばれる産業病が増えたことによって、珪砂の使用は制限されたのです。
弊社では、国際基準ISOに沿った研磨材しか使っていません。環境汚染だけではなく、作業を行なう従業員の安全も守る。当たり前のことを当たり前にやる。それが弊社の約束です。
テストブラストには取得困難な国際資格と国内資格を取得したスタッフが同席!
さらに、お客さまからのご要望にお応えするため、事前のテストブラストを実施します。その際には国際検査員資格『FROSIO(Inspector Level3)』や国内資格『防錆管理士』を取得しているスタッフが同席。下地処理後の工程までを見据えて、適切なブラスト工程をご提案いたします。
FROSIO3とは、ヨーロッパ発祥の国際検査員資格で、日本人でも限られた人しか取得できていません。もともとは船舶や海洋構造物の被塗装面の表面処理や塗装状況を検査するために生まれた資格です。弊社では、このFROSIO資格でもっともグレードが高い「Ⅲ種」FROSIO3を取得しているスタッフが在籍しています。
国家資格である防錆管理士資格と合わせて取得していますので、国際基準はもとより、国内基準にも準拠したチェックが可能です。
防錆加工処理も弊社におまかせください!

また、塗装後の防錆処理も承っております。弊社の防錆技術は国土交通省の認定技術NETISに登録されています。ブロックプライマーNと名付けられた防錆塗料は、型枠内面強化工法として登録されており、錆の抑制や耐性の強化、補修コストの軽減などのメリットが多い塗料です。
弊社では2015年にNETISに登録されました。製品によっては利用できない場合もありますが、下地加工だけではなく、塗装後の防錆加工もおまかせください!
下地加工から防錆塗装までお気軽にご相談ください!
弊社では、ブラストによる下地加工はもちろんのこと、防錆塗装まで対応可能です。定期的なメンテナンスやちょっとしたご相談であっても構いません。お気軽に弊社までご連絡ください。加工コスト削減方法についてもお気軽にご相談ください。